Unlocking Profitability: Assessing the Viability of Laser Technology for Small-Scale Production
FEATURES
3/31/20242 min read
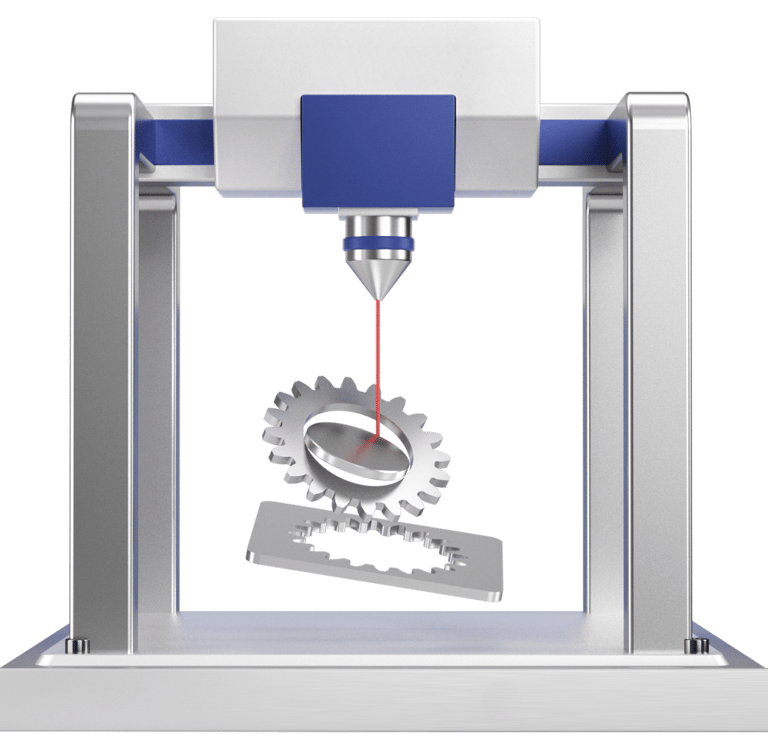
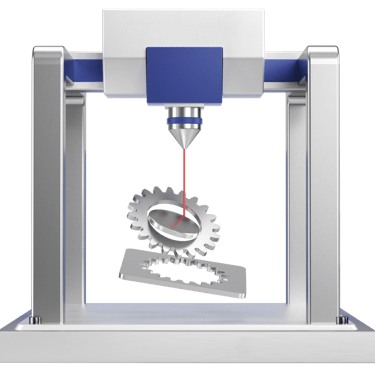
Relying on laser technology for metal cutting or marking has many advantages in practice. The processes work without contact. This protects the processed material and the tool, because a light beam does not wear out. Also, no other processing method is as flexible in terms of shaping. Tools do not have to be changed and the workpieces do not have to be clamped in time-consuming preparation. Until now however, the high purchase prices were an obstacle to using laser technology especially for cutting even for smaller quantities or prototype production. But in the meantime, there are also affordable systems suitable for such applications.
Laser systems have become established in series production to cut metal . The technology scores with high precision and quality as well as speed even the smallest cuts can be made quickly and easily. The technology is also significantly more efficient than CNC milling: with laser cutting, for example, deburring takes place automatically in the same work step. Even complex shapes or designs are no problem for the laser. No swarf is produced so there is no contamination at the workstation, and thematerial around the interface remains undamaged. In addition, handling the workpieces is simple as mechanical devices and time consuming clamping are not necessary. However, the technology often has a decisive disadvantage: the usual laser cutting systems are often too inflexible for small series or prototype production away from the inline production line. Mass production would have to be stopped for small series or prototypes, which is not justifiable for economic reasons.
An innovative stand-alone laser cutter
JustLaser has a practical solution in its program especially for applications that need flexible laser systems to cut metal and to be used as stand-alone devices outside of series production: the JustCut is a compact fiber laser system with a laser power of up to 3 kW for processing thin sheets up to 6 mm thick. It can cut a wide range of metals, such as V2A and V4A stainless steel, steel, aluminum, brass, or copper. With an optional round engraving device, it is also possible to process rounded and cylindrical workpieces such as pipes with diameters of up to 153 mm. The high-power fiber laser offers high operational reliability and beam quality as well as long-term tested reflection protection.
The laser cutter is housed in a compact enclosure, so it consumes little floor space. Thanks to its class 2 safety rating, it does not require a protective room and can be used in high-traffic areas such as busy factory floors. Two convenient sliding doors at either end of the machine provide good accessibility. Sliding access windows are also installed on both sides. The processing area inside is 1320 × 1270 mm. Powerful CNC laser software is available as an option to increase system efficiency and machine throughput, for example, using nesting and NC functions such as common line, ridge and bridge cutting, and lead-in functions. Another option is the k-vision package, a sophisticated hardware and software solution that allows printed material to be cut to a precise fit. This means that today, thanks to thecomparatively low investment, there is nothing to stop laser technology being used for smaller quantities or in prototype production, even away from automated production.
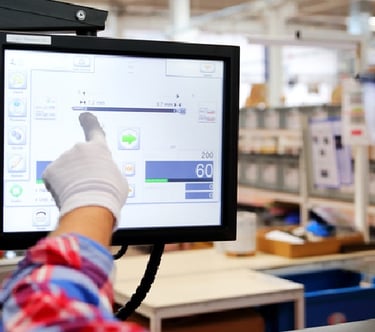
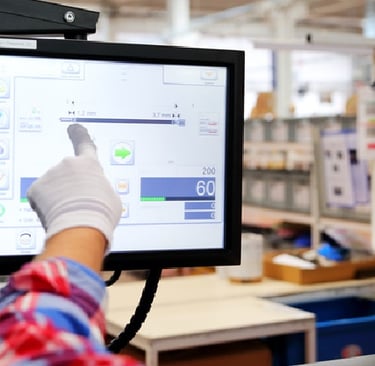
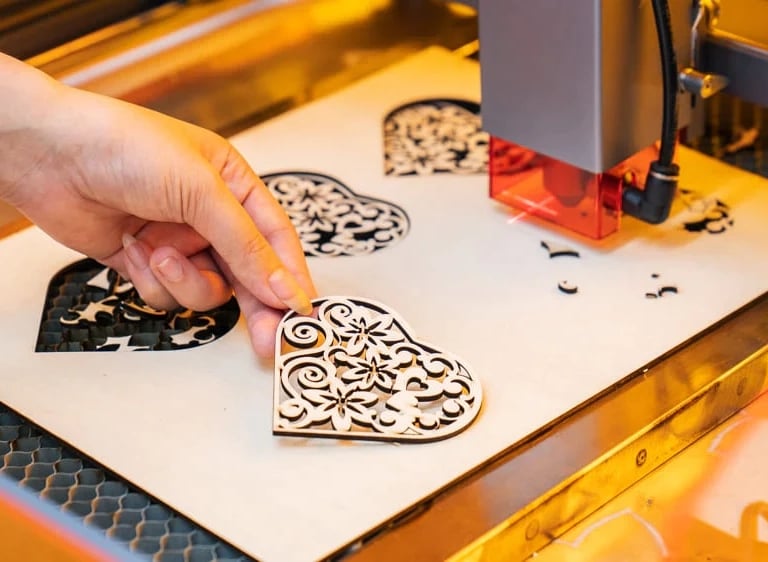
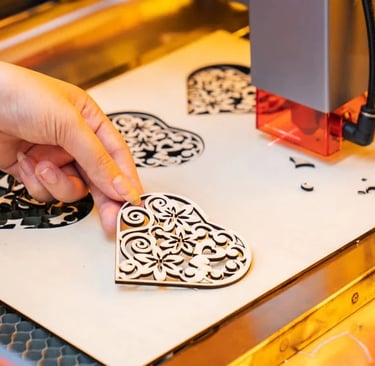